Как я реорганизовал ИТ Кыштымского Радиозавода

Вот уже скоро 60 лет в городе Кыштыме, что под Челябинском, на улице Ленина работает Радиозавод. В советское время его радиоприемники «Кварц» дарили чарующие звуки Большого симфонического оркестра Гостелерадио СССР миллионам дачников и отдыхающих на природе граждан. Предприятие одно из немногих в отрасли радиоприборостроения, которое благодаря грамотному руководителю, смогло пережить 90-е годы с минимальными потерями, а сейчас уверенно развивается.
За пять лет объем производства увеличился в десять раз, за последний год — в три раза. Сегодня среди заказчиков такие компании, как «Вымпел», МНИТИ, НПО «Прибор», ЛОМО, Машиностроительный завод им. М. И. Калинина, ОКБ «Новатор», Смоленский авиационный завод, НИИИТ «Опытный завод», ГРЦ им. Макеева, и ряд других.
Сейчас предприятие выпускает сложные радиоэлектронные приборы. По несколько тысяч детале-сборочных единиц с десятками уровней подсборок в одном изделии, с циклическим заходом деталей в один и тот же цех на разные операции.
Завод активно модернизирует производство, обновляется оборудование, открываются новые цеха. Однако до 2014 года на информационных технологиях это никак не сказывалось.
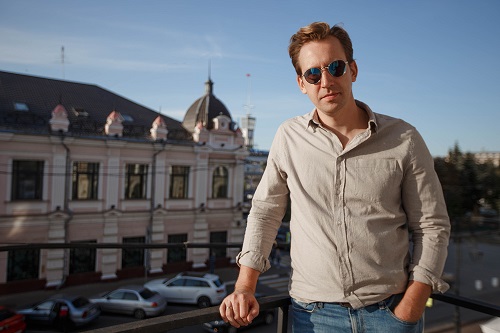
Карандашно-фломастерное бюро
Учет производства осуществлялся так: в цех выдавалась многостраничная распечатка с перечнем деталей, которые надо выпустить за смену, и в течение дня диспетчер карандашом закрашивал детали, изготовленные его цехом. Вечером кто-нибудь созванивался с планово-диспетчерским отделом и сообщал, что сделано за день. По этим данным работники диспетчерского отдела в своем экземпляре бумажного перечня также закрашивали детали.
Ну а на следующий день выяснялось, что цех деталь закрасил, а передать забыл. Или передал, а следующий цех не приступил к её обработке. И в момент сборки вечно чего-нибудь не хватало. Где детали? Начальники цехов собирались на совещание и сопоставляли, кто и что там у себя закрасил.
Сейчас на 1200 сотрудников предприятия больше 500 компьютеров (в 2014 году было 160). Но главное — это качественные изменения за счет внедрения новых информационных систем подготовки, учета и управления производством. Как это было сделано и что получилось, рассказывает Игорь Чуфаров, начальник отдела интегрированных автоматизированных систем АО «Радиозавод»:
— До 2014 года, когда я пришел на предприятие, для конструкторско-технологической подготовки производства использовалось программное обеспечение, написанное в 90-х годах прошлого века, еще под DOS. Вся автоматизация сводилась к формированию перечня деталей, который нужно было распечатать. А затем вступало в дело «карандашно-фломастерное бюро» Конечно, это было самым узким местом со стороны ИТ, и автоматизация именно данного участка предвещала самый большой эффект.
И хоть я не сторонник перевода на новые технологии ради погони за современным стеком, но в данном случае модернизация была просто необходима: система была полностью самописная, не вполне документированная, из разработчиков в штате осталась единственная сотрудница-пенсионер, кроме нее в хитросплетениях этой системы не разбирался никто. Риск для предприятия громадный.
Выбор системы
Еще до моего прихода завод приобрел систему PTC Windchill, но проект по внедрению явно буксовал. Подрядчик неустанно говорил о необходимости подписания актов выполненных работ, однако работоспособной, адаптированной под нужды предприятия системой на тот момент и не пахло.
Кроме того, поскольку Windchill закрывал только подготовку производства, вопрос об учете и управлении оставался открытым. Поэтому одновременно с операционной деятельностью я приступил к выработке стратегии развития ИТ-среды предприятия на ближайшие годы.
Основой нашей ИТ-стратегии стало не просто внедрение модной системы, а четкая цель: «Нужды производства — во главе угла».
В качестве технологической платформы была выбрана связка Windchill и 1С. Первый продукт — в силу того, что деньги уже инвестированы — надо использовать. А второй по причине наличия ИТ-специалистов даже в нашем небольшом городе и потому, что это отечественный продукт, занявший в честной конкурентной борьбе одну из лидирующих позиций в ERP-сфере. Ну и решающим моментом стал выпуск «1С:ERP Управление предприятием 2». На базе предыдущего решения — УПП 1.3, в котором учет производства был весьма условный, для нашего сложного производства ничего бы не вышло.
Освоение сотрудниками PTC Windchill было сопряжено с трудностями. Если конструкторы, технологи и отдел нормирования труда освоили стандартные механизмы Windchill, то с цеховым персоналом процесс затягивался.
Надо сказать, что в PTC знают о проблеме. Некоторое время назад компания выпустила продукт PTC Navigate, который позиционируется как инструмент для работы с Windchill смежных по отношению к конструкторско-технологической подготовке производства подразделений (снабжение, сбыт, цеха). Однако, рассмотрев в том числе и возможность внедрения PTC Navigate, я принял решение о создании инструмента, который учитывал специфику именно нашего предприятия и выводил только то, что нужно, не замусоривая интерфейс лишними функциями. Он получил название «PLM-справочник для Windchill», и это полностью наша разработка, позволяющая в режиме одного окна увидеть исчерпывающую информацию о конструкции и технологии изготовления детали или сборочной единицы.
Кроме этого, мы расширили узкие места — там, где пользователи больше всего кликали, чтобы добраться до нужной информации.
«Я передумала»
Для привыкших к карандашу и бумаге сотрудников внедрение 1С оказалось громом среди ясного неба. Культурным шоком, если можно так выразиться. На следующий день после обучения приходит ко мне кладовщица из цеха и говорит: «Я передумала, не надо мне эту систему».
Или встречаю как-то начальника одного из цехов, обучение кладовщиков которого проходило как раз накануне. И одной из кладовщиц пришлось не только объяснять работу в 1С, но и учить, как включить системный блок через источник бесперебойного питания. Спрашиваю:
— Ну как она?
— Перевел в уборщицы, пусть полы моет.
На Радиозаводе есть две особенности:
Во-первых, сложившаяся десятилетиями культура производства, в которой основным элементом информирования была бумага. Учтенная версия чертежа, выданный цеху бумажный перечень деталей и так далее. Изменить это очень сложно. Даже сейчас, имея все в электронном виде, люди подстраховываются бумажкой, потому что «так надежнее». Я понимаю это. Излишнее давление здесь плохой помощник. Пусть переход происходит в комфортном для предприятия режиме. Нет задачи поставить всех на уши и запретить бумагу. Когда сотрудник понимает, что за бумажным чертежом нужно куда-то идти и искать его, а на экране компьютера он доступен в два клика — даже консервативные люди постепенно начинают это использовать.
Вторая особенность — проекты были выполнены без остановки производства. Это как если во время движения автомобиля устаревший двигатель заменили на новый, а пассажиры продолжили ехать как ни в чем не бывало. За этим стоит наша огромная работа по непрерывной интеграции.
Связать между собой разнородные системы (отечественную и западную) — та еще задачка. Но нам предстояло не только это. Поскольку ввод в эксплуатацию происходил поэтапно (а некоторые этапы и параллельно), важно было на каждой итерации связать внедряемые системы не только между собой, но и с наследуемым программным обеспечением. Мы заменяли какую-то часть устаревшего программного обеспечения функциональным блоком нового ПО, при этом сохраняя связи с остатками старых программ.
Для пользователей, которые оставались в старых программах, ничего не менялось. Не нужно было повторно вбивать данные либо довольствоваться неактуальной информацией. С точки зрения работы пользователей все было абсолютно прозрачно.
Как бы не была проведена интеграция, если своевременно не вносить в систему данные, актуальной информации не увидеть. Оперативный производственный учет подразумевает, что нельзя мешкать. В связи с этим был принят ряд организационных мер. Есть правила, по которым межцеховая передача деталей возможна только по ордеру, выписанному в 1С. То же самое касается отчетности цехов. С определенного момента запретили предоставлять отчетность из любых источников, кроме 1С. Этим мы обеспечиваем достоверность данных. Не оформил в 1С, значит не изготовил деталь, не получил за нее деньги. Достойный мотивирующий фактор.
Скажу прямо, было все. И в том числе явный саботаж со стороны пользователей. Активно вели просветительскую работу с людьми в ходе проекта, объясняли, рассказывали. О сквозном учете, о роли каждого отдельно взятого сотрудника в этой цепочке. О том, что нельзя сделать так, чтобы все были в 1С, а один цех обходился без нее. Кардинальным же, переломным моментом стала фраза директора: «Кто не освоит работу по-новому, пойдет за ворота завода». Настрой генерального директора и главного инженера сыграл главную роль. После этого саботаж пошел на убыль, продуктивность резко повысилась. Преобразования были очень болезненными, но необходимыми во благо производства. К слову, та кладовщица, которая поначалу отказывалась работать в системе, сейчас справляется почти без ошибок.
PTC Windchill и 1С:ERP
То, что нам удалось этого добиться, — действительно высший пилотаж. Я горжусь своей командой и теми результатами, которых мы достигли.
Результаты говорят сами за себя. Информация об изделиях по всем основным заказам, выпускаемых заводом, теперь находится в Windchill. Подготовку производства всех новых заказов, коррекция состава изделия, чертежей, технологии изготовления начинаем только в Windchill. За счет этого цеха обеспечены с экрана компьютера достоверной, самой актуальной версией информации об изделии и любой детали, входящей в его состав.
А система диспетчеризации производства развернута на базе «1С:ERP Управление предприятием», все основные заказы размещены в ней, среднее количество документов в день превышает 1500, количество пользователей уже перевалило за 150. В системе ведется и учет фактической выработки сотрудников.
В конечном счете за четыре неполных года удалось перевести предприятие на современные информационные системы, с заделом на будущее, на развитие.
Сейчас Радиозавод активно развивает систему в сторону расстановки приоритетов для цехов, исходя из актуальных потребностей сборочно-монтажных подразделений. То есть, по сути, уже занимаемся реорганизацией бизнес-процессов, с учетом современных тенденций управления производством. А обеспечивает такую возможность именно внедренная передовая система на базе PTC Windchill и 1С:ERP.
О себе
Я родился в тут же, в Кыштыме (примерно 50 тысяч жителей, три крупных промышленных предприятия). В 2007 году окончил с красным дипломом Южно-Уральский государственный университет по специальности «управление и информатика». Параллельно с учебой работал. Совмещение работы и обучения переросло у меня в принцип непрерывного образования: Я посещаю профессиональные конференции Infostart по управлению и технологиям автоматизации учета на платформе «1С:Предприятие», повышал квалификацию в Уральском Федеральном университете им. Б. Н. Ельцина, проходил сертификацию учебном центре при МГТУ им. Н. Э. Баумана. Совсем недавно прошел повышение квалификации в Высшей Школе Экономики в Москве по теме оптимизации бизнес-процессов. Для нас эта тема очень актуальна, поскольку автоматизация открывает огромные перспективы для реинжиниринга процессов.Сейчас обучаюсь на совместном курсе ЮУрГУ и Академии AFW Wirtschaftsacademie Bad Harzburg GmbH (Германия) «Управление проектами». Готовлюсь к аттестации на получение Гарцбургского сертификата “Projektmanager/in”, заверенного госдепартаментом образования Германии.
Кроме обучения, и сам с удовольствием делюсь наработанным опытом с коллегами по отрасли — в ноябре выступал с докладом на форуме «Передовые технологии автоматизации. ПТА-Урал 2018», где рассказывал об опыте внедрения PTC Windchill и «1С:ERP Управление предприятием» на АО «Радиозавод».
Начинал карьеру в небольшой фирме по производству и обслуживанию домофонов. После этого работал на одном из предприятий холдинга «Группа Магнезит», где вырос от специалиста по программному обеспечению и обслуживанию компьютерных установок до начальника отдела информационных технологий.
В 2014 году пригласили на Радиозавод на должность начальника отдела интегрированных автоматизированных систем. Радиозавод — это предприятие с самыми лучшими перспективами в городе. Конечно, я согласился.
Опубликовано 16.01.2019